The Irvin Air Chute: Life Preserver of the Air
Leslie L. Irvin, shown wearing one of his parachutes, 1930s. Image source: private collection.
Leslie L. Irvin, after whom the Irving Air Chute Company was named, was born in Los Angeles, California and became a stuntman for the movie industry. He made his first parachute jump from an airplane at age 14. His nickname became "Sky-Hi Irvin.' His wife later said, "The air was his whole life. He had no other amibition beyond the next jump, the next balloon trip."
Irvin did not invent the parachute, but he worked ambitiously on developing a parachute that could be worn by the user and operated by a manual ripcord, the opposite of the static-line "automatic" parachutes of the day. When he demonstrated a silk version of his parachute design in April 1919 in Dayton, Ohio, he was awarded a military contract by the U.S. Army. What had begun as a prototype created on a borrowed millinery sewing machine in Buffalo became the "Irving Air Chute Company" in June 1919. (The company name was the result of a typographic error and remained until 1970.) Leslie Irvin was 24 years old at the time.
The first Irving factory was created in Buffalo. In 1928, 50 parachutes were manufactured per week. According to Flight magazine (October 11, 1928), "The manufacture of parachutes does not call for greatly skilled labour; it demands rather extreme care and caution." Each raw material component was tested before being used: the harness cord, webbing, snaps, buckles the silk, even the thread.
The company grew quickly because it had few competitors and in the 1920s and early 1930s nearly every parachute used was made by Irving Air Chute. In 1925, the Royal Air Force of the United Kingdom ordred Irving parachutes for its airmen. Leslie Irvin moved to England in 1926 to operate a new Irving factory in Letchworth as vice-president.
George Waite, Buffalo factory president. Image source: Life Magazine, private collection.
In Buffalo, George Waite, a former silk dealer, was president of the company; he never parachuted and believed they should only be used in an emergency.
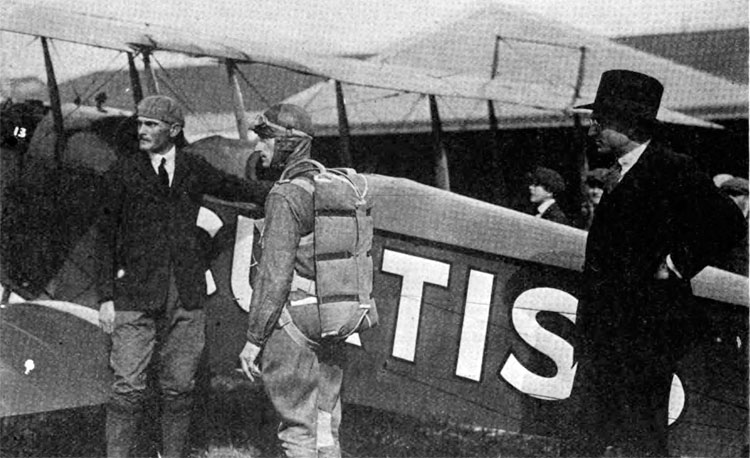
Leslie Irvin at right beside a pilot and parachuter (and Curtiss plane) in June 1920. In that year, the Irvin Air Chute won the Aerial League of America's Aerial Safety Trophy. Image source: Flying magazine, June 1920.
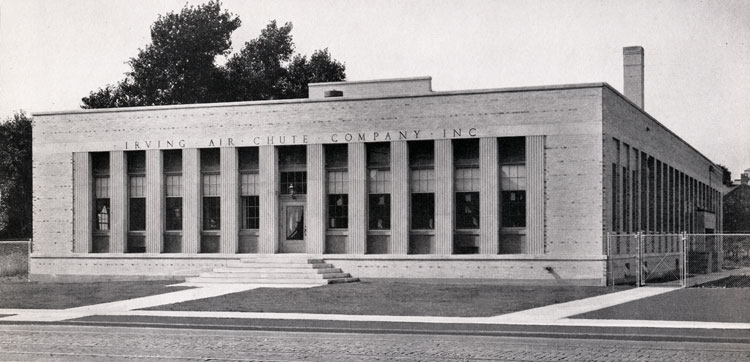
The Buffalo Irving Air Chute factory at 1670 Jefferson Avenue. Image source: private collection.
Cover of LIfe Magazine, March 22, 1937, featuring Irving Air Chute Company. Image source: private collection
The Irving Air Chute Company was the cover story for the March 22, 1937 Life Magazine. The seven-page story featured photos of parachutists using the chute as well as the rubber dummy (cover photo) utilized for testing each parachute.
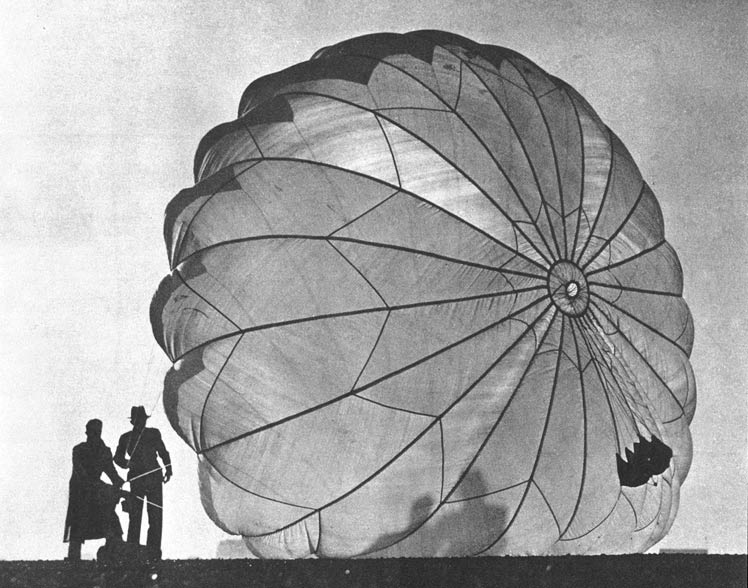
Backlit photo showing the design of the Irving parachute. Photo taken for Life by Margaret Bourke-White, 1937.
Image source: Life MagaIne, private collection.
"Irving Air Chute's chief asset is its patented folding technique which insures the parachute's opening. Its bias construction gives it more strength than other types and is its distinguishing feature. A 24-ft. Irving chute is made of 24 panels, each manufactured in four sections cut on a bias. Thus if a rip starts it must go across all threads and will quickly dead-end against a seam. All seams consist of four thicknesses of material sewn together with a very strong thread (tensile strength: 8 1/2 lb.). When all the seams are joined together, two rows of one-inch silk tape (tensile strength: 300 lb.) are put around the top (or vent) of the chute, one row around its skirt. Shroud or ratlines are brought down through each seam but before they are inserted, they must be pulled to a uniform tension. This is done by laying them on a table and pulling them around rollers to a tension of 625 lb., thus assuring an equal pull all over. When completed, each chute is tested twice before packing and numbering." (Life article, March 22, 1937)
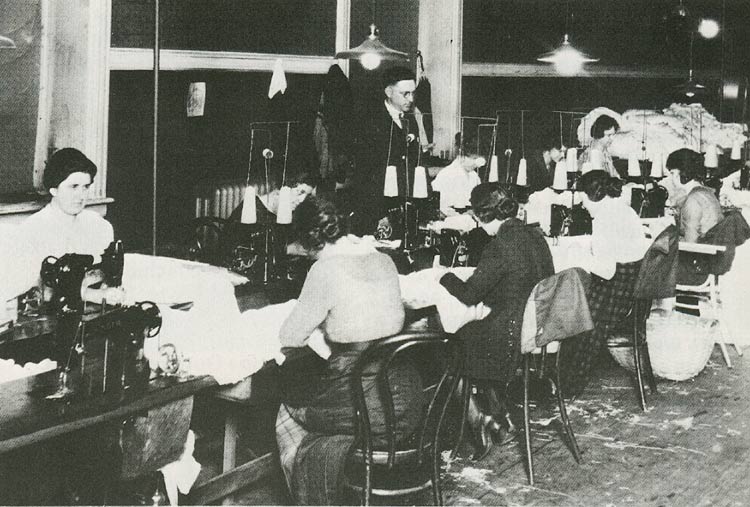
Buffalo Irving Air Chute employees at work sewing silk parachute sections. Leslie Irvin is standing, center.
Image source: "Buffalo Airport, 1926-1976".
Steps in packing Irvin parachute at the Buffalo factory, 1937, in Life magazine. Image source: private collection.
"For U.S. Government use Irving must use, whenever possible, domestic materials. Ordinarily, Japanese silk is preferred. Last year Irving used 125,500 yards of silk and a ton of silk thread in filling its orders. Its peack production was 124 parachutes a week, each one worth about $350. Net sales for 1936 totaled $1,345,418."
Life article, March 22, 1937
In July 1940, as part of its promise to end U.S. dependence on silk (and Japan), Irving Air Chute delivered to the government an experimental order of parachutes made from DuPont nylon.
Prior to World War II, the Army required each Irving parachute to be drop-tested before shipped. In the early 1930s the Kenny Flying Serivce had the contract for two drop-tests of every parachute. Later the Buffalo Aeronautical Corporation was awarded the contract, using a Ryan monoplane with a hole cut in the floor, through which the 180-lb solid rubber dummies were dropped. The plane made as many as 50 trips per day.
Pressure to supply large quantities for the war forced a shift to new testing methods and better quality control, thus eliminating the need to drop-test each parachute.
Right: Irving Air Chute employees preparing dummies for the required test drop of the Irvin Air Chute, 1937, in Life magazine. Image source: private colleciton.
Left: Irving Air Chute employees airing the silk parachutes, 1937, in LIfe magazine. Image source: private collection
Silk parachutes were susceptible to decay when stored packed and so they had to be aired every two or three months to prevent mold or sweating. The photo at left is of the interior of the Buffalo factory.
By 1939, 45 foreign countries were using Irving parachutes, including Germany, which had confiscated an Irving plant and bought its patents in 1936.
The paratrooper landings of the Allied forces on D-Day were made using Irivng parachutes.
Cover of a company booklet advertising the different types of parachutes made by the company, c. 1945-49. Image source: private collection.
The company expanded, opening a plant in Lexington, Kentucky in 1942, Fort Erie, Ontario in 1945, Glendale California in 1949. The Buffalo factory was expanded in 1950 and then closed in 1953; the age of the plant and union challenges were cited as reasons for the closure. Local production was moved to the Fort Erie factory.
Leslie Irvin, who had moved back to the U.S. to manage the company after George Waite's retirement in 1946, moved home to California with his wife in the 1960s. When he died in 1966 at age 71, his obituary called him, "Father of the Parachute."
The Irvin Air Chutes company became Irvin Industries in 1970, Irvin Aerospace in 1996, and then merged with other companies in 2007 to become Airborn Systems. Among many other products related to the aviation industry, the company still makes parachutes.
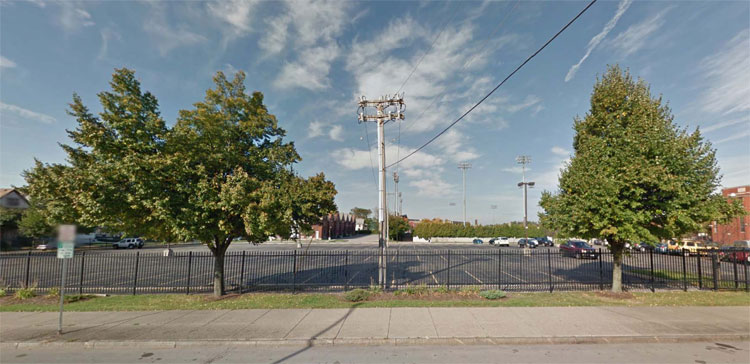
The Irving Air Chute factory at 1670 Jefferson was demolished and is a parking lot.